In the dynamic landscape of industrial operations, investing in a world-class industrial shredder is a pivotal decision for companies seeking efficiency and sustainability. The returns on this investment are multifaceted, spanning labor savings, expanded production floor space, and the reduction or elimination of landfilling costs. Notably, these cutting-edge machines play a crucial role in fostering responsible stewardship of raw materials by transforming waste—such as wood, paper, and plastics—into valuable by-products. However, safeguarding these indispensable assets from potential damage is paramount. The threat of tramp metal, encompassing foreign ferrous materials accidentally mixed with the intended scrap, looms large. Cresswood Shredding Machinery, a frontrunner in the industry, has integrated a revolutionary solution to this challenge—effective metal detection. This blog delves into the significance of this protection feature and the recent transition to American-made metal detection solutions from Metal Detectors, Inc. (MDI). Join us on this journey as we explore the enhanced capabilities and peace of mind that MDI’s metal detection technology brings to our world-class industrial grinders.
Protecting Your World Class Industrial Grinder Investment
A quality industrial grinder is a significant investment for companies to make. Even so, the ROI is nearly always worth the investment, coming in the form of labor savings, opening up production floor space, and the reduction or even elimination of landfilling costs. Yet another huge benefit is in creating better stewardship of raw materials, preventing the needless landfilling of wood, paper, and plastics by transforming the waste into valuable by-products.
As with any essential production asset, every step should be taken to protect these valuable pieces of equipment from unnecessary damage due to improper use. Tramp metal comes in many forms, and can cause immediate and serious damage to any industrial grinder. Tramp metal is a generic description of any foreign ferrous material being accidentally mixed with the scrap intended for grinding/shredding – things like chain hooks, crowbars, hammers, or large hardware. I’ve even seen a load of crated engine block manifolds that got inside one of our hopper-fed grinders! Once this foreign material gets into the rotating cutter head, it can inflict damage to tooling, tooling holders, screens, and drivetrain elements like pulleys, gearboxes, and drive-shaft keyways. These can be expensive fixes and add unnecessarily to the overall cost of ownership, not to mention the headaches from all the unplanned downtime. In the flooring industry, for example, grinders are integrated into highly automated saw lines and generally are discharged into air systems. Tramp metal in this environment can also pose the risk of sparks being generated that make their way into the dust collection system. Metal detection becomes a “must-have” option in scenarios like these to prevent risk of fire.
Cresswood’s Advanced Metal Detection Integration in Industrial Grinders
Cresswood Shredding Machinery has integrated many critical improvements with machine protection features, one of the most important being effective METAL DETECTION. With a horizontally fed industrial grinder, the material is always introduced into the grinder via a paired vibratory conveyor. A metal detection unit can easily be placed within this system to find any ferrous material that happens to get into the scrap mix, preventing it from getting to the grinder itself and thus eliminating the potential damages from tramp metal. On vertically-fed industrial grinders, a tunnel-style metal detection unit or an over-band magnet can be integrated into the in-feeding conveyor to achieve the same type of protection.
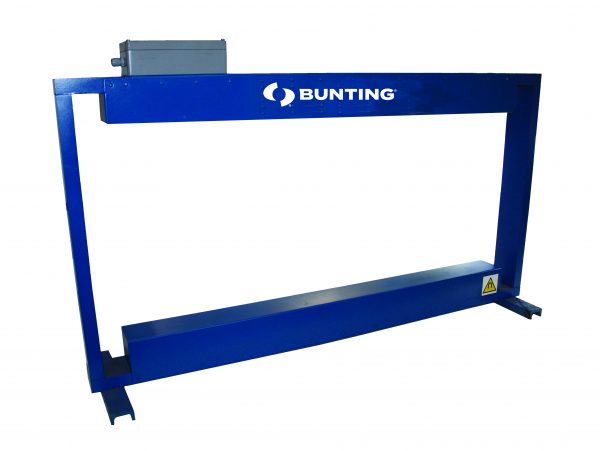
Example of tunnel-style metal detector for infeed conveyor
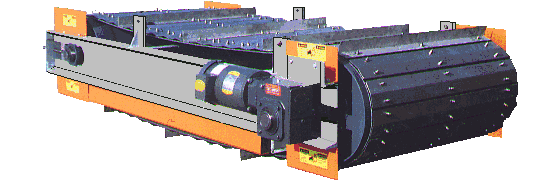
Example of over-band magnet
Safeguarding Industrial Grinding Processes with Precision and Control
The heart of the detection unit is referred to as a search coil, a sophisticated piece of electronics that creates invisible magnetic fields that envelop the area above it. All the material on the conveyor must pass over and through these magnetic fields before being ground. Any ferrous contamination in the mix will pass over the search coil and immediately interrupt these fields. The sophisticated control unit constantly monitors the magnetic fields and picks up any of these interruptions. If metal is detected, a signal is instantly sent to the grinder control panel telling it to shut down the conveyor, stopping the flow of material in its tracks. An operator can then find and remove the metal object and safely restart the system. The control can easily be fine-tuned to work within the environment and detection parameters the particular grinding application demands.
Because the sensitive control on a metal detector uses electronic signals to detect ferrous contamination, it can become confused by electromagnetic interference (EMI) in the production environment it operates in. Proper grounding and adequate protection from electronic “noise”, especially that which is generated from variable frequency drive (VFD) motors or power lines, are essential. If these steps are not taken, the protective feature can quickly become a serious nuisance. With the advances in automation and material conveyance in most production settings, the modern factories of today have much more EMI than they did in the past. Some metal detection technologies that worked fine in the past in low EMI environments may not function properly in a modern factory setting full of VFD drives and other sources of electronic noise.
Cresswood’s Transition to Cutting-Edge MDI Metal Detection Solutions for Enhanced Performance and Precision
Cresswood found itself having to change from an outdated metal detection option because it no longer served reliably in several applications with high EMI. We are passionate about our commitment to our customers and it wasn’t acceptable to offer a “solution” that didn’t meet or exceed our client’s expectations in every circumstance. We decided we had to switch vendors and went with the best the industry had to offer, American-made metal detection solutions from MDI. Proudly made in Eugene, Oregon, USA, Metal Detectors, Inc. has been a proven leader in industrial Metal Detection technology since 1965. With their experienced in-house design, manufacturing, and product support team, we felt confident MDI could provide Cresswood with excellent products for all of our horizontal industrial grinders. With the MDI solution, the search coil is integrated into a rugged fiberglass section, providing an entire section of the conveyor that is completely non-ferrous. This isolates the magnetic fields of the search coil from any incidental interference from the steel vibe assembly and the VFD drive motors on the grinder and conveyor system. MDI also offers a high-performance control module upgrade specifically engineered to work within high EMI environments. Frequency isolation options on the control module allow the identification and selection of quiet frequencies to operate within that are not shared by VFD motors nearby.
Internal testing has revealed this solution offers significantly enhanced metal detection options that are specifically engineered to operate flawlessly within high levels of electronic interference. It is also equipped with a control module that allows the user to fine-tune frequency and detection parameter settings. The unit can discover large ferrous objects like rotors, wrenches, hammers, and heavy steel screws, right down to small objects like lock washers. These features ensure this option provides the peace of mind of a useful and effective protective feature, while not becoming a nuisance that is inevitably bypassed by the production staff who have to work with it every day. This change is yet another testimony to Cresswood’s relentless commitment to the customer with product excellence and innovation.
As we embark on this new chapter, we are excited to bring MDI’s cutting-edge metal detection technology to our customer’s production lines, enhancing the reliability and performance of our world-class industrial grinders. With this advanced protective feature, we reinforce our commitment to providing top-notch solutions that align with the evolving needs of modern manufacturing environments. Together, we shape a future where industrial operations thrive with efficiency, sustainability, and unparalleled reliability.
Recent Comments